Automation is no longer the future—it’s the present. Across countless industries, robotic technology is changing how work gets done.
One of the most transformative combinations in modern manufacturing is the integration of robots and welding, offering unprecedented speed, precision, and reliability in production environments.
The rise of smart factories and digitized production systems makes robotic welding a central pillar in global manufacturing. Companies that delay adoption risk falling behind more agile competitors.
Key Points:
- Robotic welding brings unmatched consistency, speed, and accuracy to fabrication.
- Human welders are still essential but are now focused on complex, skilled work.
- Robotic systems reduce scrap, rework, and production delays.
- Smart automation reduces costs and increases productivity in the long run.
- Every successful integration must be customized to fit plant-specific needs.
- Future welding robots will feature adaptive learning and cloud-based control.
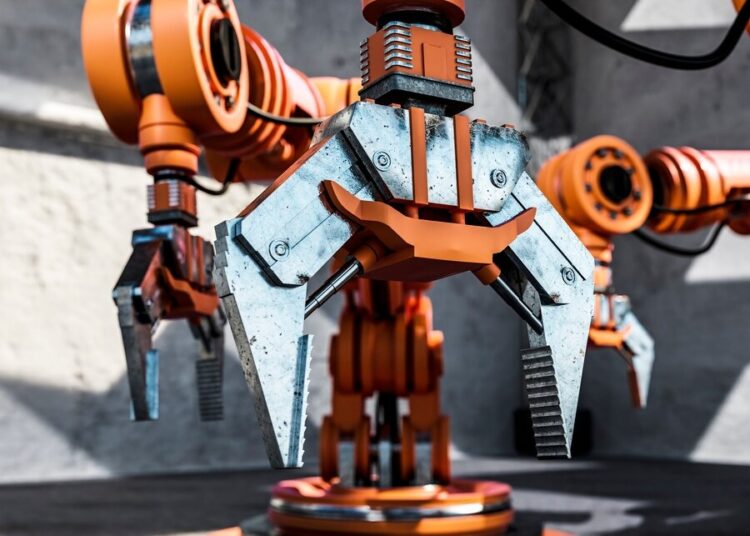
What Makes Robotic Welding So Effective?
Traditional welding is highly skilled, physically demanding, and time-consuming.
While human expertise remains valuable, robotic welding introduces several enhancements that traditional methods struggle to match.
With advanced programming and motion control, robots can execute highly precise welds across a variety of materials and geometries.
Unlike manual welding, robots can deliver consistent quality across high-volume production lines.
They don’t suffer from fatigue, variations in technique, or workplace distractions—making them ideal for operations that demand unwavering accuracy.
Key Advantages for Modern Manufacturers
The benefits of integrating robotic welding solutions are clear and wide-ranging:
- Reduced Errors and Rework: Robotic welders consistently meet tight tolerances, minimising mistakes that lead to scrap or repair work.
- Faster Turnaround Times: Robots can weld at higher speeds than humans and operate continuously, significantly increasing throughput.
- Lower Long-Term Costs: Though the initial setup cost can be high, reduced labour expenses and improved process efficiency lead to strong ROI.
- Better Use of Skilled Labour: With robots handling repetitive tasks, skilled welders can be redeployed to more complex and value-added roles.
Strategic Implementation
For businesses looking to adopt robotic welding, it’s essential to consider workflow, part design, and production goals.
A well-integrated robotic solution doesn’t just drop into place—it’s tailored to fit the unique needs of a facility.
Factors such as space constraints, materials used, and cycle time requirements must all be accounted for.
This is why choosing an experienced partner is crucial.
Cyber-Weld, a leading UK provider of automated welding solutions, offers comprehensive support for manufacturers ready to embrace the future of fabrication.
Their services cover everything from system design to ongoing support.
You can learn more about their work in robots and welding through their dedicated integration page.
How to Prepare Your Facility for Robotic Welding
Before installing robotic welders, manufacturers must prepare their environments to support automation.
Preparation reduces downtime, avoids compatibility issues, and ensures a smoother transition from manual to automated workflows.
Steps to get started:
- Assess Current Infrastructure – Identify equipment, layouts, and support systems that need modification.
- Evaluate Part Consistency – Robotic welders need uniform parts for optimal performance.
- Train Your Workforce – Upskill existing employees in robot operation and maintenance.
- Plan Maintenance Routines – Build a schedule that avoids disruption and keeps equipment in peak condition.
- Engage a Reliable Integrator – Work with partners who specialize in seamless deployment.
Making your facility robot-ready is a project in itself. But without this groundwork, even the most advanced system can fall short of expectations.
Industries Leading the Way in Robotic Welding
Robotic welding isn’t limited to automotive manufacturing. Several industries are expanding their use of robotic systems to stay competitive in a global market.
Some are already benefiting from faster lead times, fewer errors, and better margins.
Top adopters include:
- Automotive – Large volumes and repeatable designs make this sector ideal for automation.
- Construction Equipment – Heavy, complex parts benefit from robotic consistency and strength.
- Shipbuilding – Precision and scale demand robotic reliability over human fatigue.
- Aerospace – Requires ultra-precise welds with no margin for error.
- Agricultural Machinery – Durable, custom components call for flexible automation.
These industries set the benchmark. But smaller manufacturers are also catching up by adopting scaled-down, modular welding cells suited for low-to-mid-volume production.
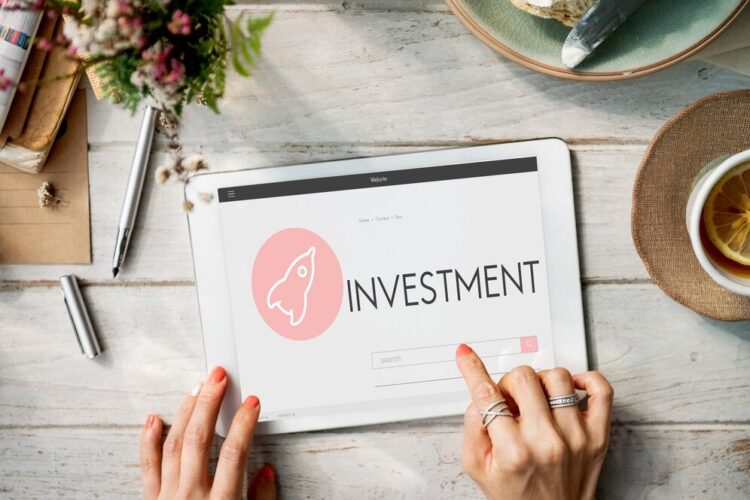
Maximizing Return on Investment with Smart Planning
Initial setup costs may feel daunting, but smart planning helps shorten payback periods and increase profit margins.
The key lies in designing a process that avoids over-investment and adapts over time.
Recommendations for high ROI:
- Start Small – Use one robot on a high-volume part to prove value.
- Track KPIs – Monitor downtime, throughput, error rates, and repair frequency.
- Scale Gradually – Add systems based on growth and need.
- Upgrade When Needed – Integrate sensors or AI modules only when they support goals.
- Document Everything – Keep detailed records of integration phases and performance gains.
When implementation aligns with clear targets, robotic welding pays off not just in savings—but in speed, safety, and reputation.
Looking to the Horizon
As automation technology continues to evolve, robotic welding systems will become smarter, more versatile, and even easier to implement.
Features like real-time feedback, adaptive learning, and cloud-based monitoring are already becoming mainstream.
These developments will further cement robotic welding as a cornerstone of efficient, future-ready manufacturing.
Companies that fail to modernize may soon find their workflows—and profit margins—left behind. Robotics isn’t just an upgrade anymore. It’s the new minimum for staying relevant in fabrication.